Wigan Album
Bickershaw colliery
5 Comments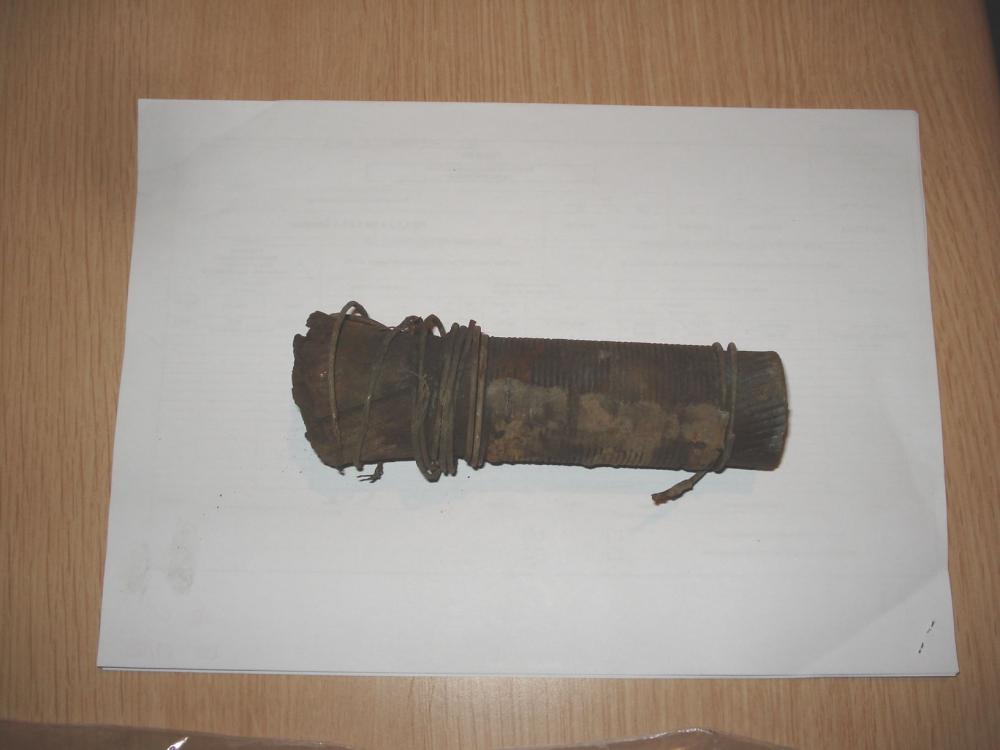
Photo: John Taylor
Item #: 22478
Once a year during a maintenance shutdown, the winding rope would be “capped” by the blacksmith. This procedure saw the cage held at the top of the pit shaft on a temporary bridging girder stretched across the shaft walls, so that the weight of the cage was off the rope, and a six foot length removed and then sent for testing at Walkden. This piece is just a small section of the portion that would have been removed. I understand from what has been said that every two years the whole rope would be changed as a matter of course with the twelve month check mentioned above, done as an interim precaution. When the rope was to be replaced by a new one and due to the colossal amount of work necessary it would “be all day of a job”. During the days of steam winding, due to the laborious work required to wind the new replacement rope onto the winding drum slowly, literally “inching it round” very gradually so that it lined up with scrolled helix cut into the face of the drum; it was standard practice to have two winders on duty during this procedure; so physically debilitating (or “knackering” of course in pitman’s parlance) was it!
No.3 shaft was around half a mile deep – 2600 feet – so one can imagine the sheer physical graft involved in removing the old rope a landing the new rope!
Approximately one and a half inches in diameter, and made of high tensile steel, it is a multi stranded wire rope. The rope is actually made up of around 9 layers of wire each one wrapped around the preceding lay, the overall circumference of the rope becoming successively larger as each lay is added to it. Each single strand is around 1/8th on an inch in diameter.
This method of construction forms a very strong, yet flexible rope.
Your clear explanation makes me realise just how little I know (knew) about just one (albeit extremely important) facet of mining technology. Thank you for giving me an insight I would otherwise never have come across.
Thanks for that John, I couldn't agree with you more. The sheer ingenuity and skill that went into an enterprise like this is is astounding, I am just glad Harold is able to share knowledge like this before it disappears altogether. Shame on Margaret and the Tories for all that she/they did to a once proud and mighty coal industry.
Wasn't it No. 3 Pit where an overwind happened (long time ago), where the ascending cage was dragged into the top of the headgear, the rope was pulled out of the capping and smashed through the engine house roof. The descending cage smashed through the timbers at the pit bottom and some of the men were drowned?
Yes that's correct Nev. Here is a link which provides some more information to the accident in 1932. The sheer terror suffered by the sole survivor who narrowly avoided the fate of his ninteen compatriots who all drowned is probably hard to for us to imagine. Tough chaps is all I can say.
This time with links attached - DOH!!
http://www.leighlife.com/index.php?action=mgallery;sa=item;id=9782
http://www.healeyhero.co.uk/rescue/pits/Bickershaw/Bickershaw1.html